19 Types of Cement
Following are the 19 types of cement classification:
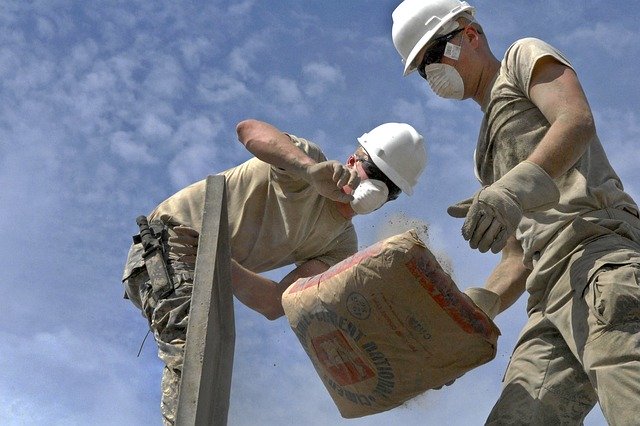
1. Ordinary Portland Cement
It is obtained by burning (at about 1450 degrees centigrade) calcareous, siliceous, and argillaceous raw materials mixed in definite proportion and crushing the resulting clinker to a fine powder.
- Ordinary Portland Cement 33 Grade– IS 269: 1989
- Ordinary Portland Cement 43 Grade– IS 8112: 1989
- Ordinary Portland Cement 53 Grade– IS 12269: 1987
2. Portland Pozzolana Cement
In the case of manufacturing of portland pozzolana cement, about 30 per cent of pozzolanic material is added to the ordinary cement clinker and the mix is thoroughly grounded. The pozzolanic material used are calcined clay or fly ash.
3. Super Sulphated Cement(IS 6909: 1990)
Super sulphate cement is made from well-granulated blast furnace slag of about 80 to 85 %, calcium sulphate of around 10 to 15 %, and Portland cement of about 1 to 2 %. The mixture of all these components is then grounded finer than the Portland cement.
4. Rapid Hardening Cement – IS 8041: 1990
As the name suggests, It hardens by gaining its strength faster than the ordinary Portland cement, because it has a higher percentage of C3S content, with finer grinding. The fineness value of rapid hardening cement is 325 kg/cm2 which is more than of OPC fineness value.
5. Extra Rapid Hardening Cement
6. Sulphate Resisting Cement – IS 12330: 1988
7. Portland Slag Cement
Portland slag cement is obtained by mixing Portland cement clinker, gypsum and granulated blast furnace slag in suitable proportions and grinding the mixture to get a thorough and intimate mixture between the constituents.
Characteristics of slag cement
➤ The fineness value of P.S.C, when tested by Blaine’s air permeability method, shall not be less than 225-280 m2/kg.
➤ The expansion value (i.e. soundness) of Un aerated cement when tested by Le-Chaelier method shall not be more than 10 mm and when tested by the autoclave method shall not be more than 0.8%.
Advantages of slag cement
Following are the advantages of slag cement
⇰ Reduced heat of hydration;
⇰ Refinement of pore structure.
⇰ Reduced permeability
⇰ Increased resistance to chemical attack.
⇰ Increasing strength and durability.
Disadvantages of slag cement
⇰ Strength gain is slow
⇰ In cold weather conditions, the low heat of hydration of slag cement coupled with moderately low rate of strength development can lead to frost damage
What are the uses of slag cement?
⇰ Producing concrete blocks with slag cement.
⇰ Slag cement is used in high-performance concrete.
⇰ Producing pre-cast and pre-stressed concrete with slag cement.
⇰ Slag cement is used in concrete pavements.
8. Quick Setting Cement
9. Low Heat Cement – IS 12600: 1989
10. Air Entraining Cement
11. Coloured Cement: White Cement – IS 8042: 1989
White cement is just a variety of ordinary portland cement, it is white in colour. The whiteness is obtained by reducing the iron oxide content to a minimum. The properties of white cement are the same as ordinary portland cement.
What are the uses of white cement?
It is generally used for decorative work, such as terrazzo flooring, face plasters, marking etc.
12. Hydrophobic Cement – IS 8043: 1991
13. Masonry Cement – IS 3466: 1988
14. Expansive Cement
15. Oil Well Cement – IS 8229: 1986
16. Rediset Cement
In some cases, time is a very important factor. Such as rapid repair of the road, repair of pavement, etc. In such cases, cement should be such that it could achieve high strength in a matter of hours. There is no doubt that High aluminium cement is one that fulfils all the above requirements, but it has also some limitations. It cannot be used in hot weather and in humid regions. So a new type of cement was needed to fill this gap.
For that reason, In the PCA laboratories of the USA began their investigation to develop a new type of cement. And, finally, they developed a cement called Regset Cement. After that, in India, Associated Cement Company (ACC) company developed a similar type of cement which is called “Rediset Cement“.
Rediset cement is able to gain high strength in a matter of hours, without showing any retrogression.
17. Concrete Sleeper grade Cement
18. High Alumina Cement – IS 6452: 1989
This cement is also known as aluminous cement. It contains as high as 35 to 45 % of aluminates. This cement is manufactured from bauxite and chalk or limestone. This cement is very dark in colour. In this cement, setting time is controlled by the rate of cooling of the fused product and not by adding gypsum.
Characteristics of high alumina cement
Following are some important properties or characteristics of high alumina cement:
➤ Its initial setting time is 3 to 6 hours and the final setting time is 8 to 10 hours.
➤ This cement gains strength very quickly, due to the presence of a high percentage of aluminates. In 24 hours it gains as much strength as an ordinary cement acquires in 24 days.
➤ This cement is very much resistant to sea water attacks as well as chemical attacks.
➤ Its compressive strength is almost double that of ordinary cement.
➤ There is no trace of free lime and hence, this cement is more sound than ordinary cement.
What are the uses of high alumina cement?
⇰ It is used for constructions near sea shore and also underwater.
⇰ It is also used for making hard and heat-resistant concrete.
⇰ It is used for sealing rocks or concreting against internal water flow.
19. Very High Strength Cement
Read More: