Human ancient history has witnessed some great monuments and engineering marvels which were considered impossible at that time period.
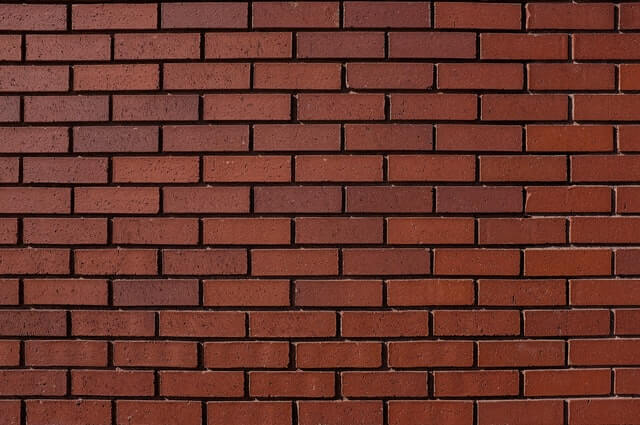
Our ancestors, nearly thousands of years ago, were using techniques that are still a mystery in the modern day, but something was still common in most of these structures which acts as a link between modern and ancient engineering. “Brick” is that link.
Humans have been using bricks for almost thousands of years and they are still one of the most important materials in any construction.
It is believed that brick was invented around 7000 BC, and it is the oldest known building material to mankind. Even though it is ancient, bricks are the number one choice in any construction assignment.
It is also one of the most durable materials and very versatile. For better efficiency bricks should be smaller in size and should have manageable weight for the labourers to pick the bricks effortlessly.
Bigger bricks are made for thicker walls. Historically, it was believed that bigger bricks were necessary for colder regions, while smaller bricks are economical and efficient in warm climatic regions.
A correct brick can be picked by observing its colour, surface smoothness, density, weight, absorption, pore structure, thermal characteristics and fire resistance.
A slightly bigger brick requires less mortar and time, which reduces cost. The use of brick has declined due to concerns about earthquake resistance.
To overcome this problem bricks along with steel reinforcements are used to make better protection against earthquakes. This type of brickwork is well known as reinforcement brickwork.
Generally, the compressive strengths of the bricks range from 1.5 to 12 N/mm2.
The process of making brick is still the same as it was first produced. The first brick was made in warm climates, clay mud was shaped into bricks and then sun-dried for hardening.
After this, the concept and process of fire bricks were discovered, which is relevant still today.
Bricks are used to construct roads, walls, and mostly for the construction of buildings. During the industrial era, the production of bricks started massively. Bricks were preferred over stones because of their lightweight and economical prowess.
Mostly bricks were produced by the hand-molding method until Henry Clayton patented his first brick-making machine. This led to a revolution in the brick industry because this machine was producing 25,000 bricks per day without any detailed supervision.
Different Types of Bricks
Bricks are versatile and easy to use which is the main reason for their popularity all over the world. It is manufactured generally in a rectangular shape using clay. Today, there are different types of bricks used in construction, depending upon the materials used, like concrete, lime, ash and many more. Let us take a look at its types.
- SUN-DRIED BRICKS
- BURNT CLAY BRICKS
- FLY ASH BRICKS
- CONCRETE BRICKS
- ENGINEERING BRICKS
- CALCIUM SILICATE BRICKS
- POROTHERM BRICKS
1. SUN-DRIED BRICKS
These are simple mud bricks, dried in the Sun for hardening. It is the most important building material that has been used since ancient times. These bricks are very similar to Adobe. Adobes are mostly used in Arizona and New Mexico.
The way to make it is very simple. At first, a shallow hole is prepared by the workers. Then earth and water are mixed thoroughly into the hole. Straw or loam is added during mixing to get sticky mixed.
When the clay achieved the desirable firmness, it is poured and shoved into open moulds and then taken down properly. These moulded bricks are then left to dry thoroughly in the Sun.
In ancient times, bricks were generally sun-dried because of the unavailability of timber fuel.
2. BURNT CLAY BRICKS
These types of bricks are the most widely used brick, and one of the most ancient bricks used as construction material. These bricks have a much superior quality compared to sun-dried bricks. They are used for all types of works such as walls, columns, foundations, etc.
They are persistent to moisture, insects, and erosion. They create a good environment for the room and have medium to high compressibility. These bricks can be made with factory sophisticated methods, simple labour methods, or a range of mechanized technologies.
Labor-intensive methods are most suitable for rural areas, as the demand for these bricks is limited because of the lesser population. Handmade bricks would generally lack in quality and compressive strength. Handmade bricks are most likely to have irregular dimensions.
But, these labour-intensive handmade bricks are economical and require very little investment capital and transportation cost. The four most important ingredients for making bricks are suitable clay, water, fuel, and manpower. Burnt bricks are classified into four different types;
First-class Bricks:
The first-class bricks have all the superior quality of bricks. These bricks are table molded and are burnt in kilns.
=First-class bricks have smooth surfaces.
= They are rigid.
= The edges are sharp,
= They are very durable.
= They have superior strength and compressibility. Read more – Characteristics of First Class Bricks
Second class Bricks:
The Second-class bricks are inferior to first-class bricks in quality and strength. They have a moderate quality. These bricks have somewhat rough surfaces and irregular shapes as compared to first-class bricks. Few cracks could also be observed with keen eyes which is proof of its moderate quality which is inferior to first-class bricks. These bricks are used where it is covered with a layer of plaster. Read more – Characteristics of Second Class Bricks.
Third-class Bricks:
The third-class Bricks are mostly used for temporary structures. These bricks are very poor in quality. They are more porous i.e. they absorb rainwater more than any other bricks available. These bricks are inferior to both second-class and first-class bricks. They have rough surfaces and edges are most of the time broken or uneven.
Fourth class Bricks:
These bricks are mostly disregarded bricks. They have irregular, rough, over-burnt surfaces, and have darker colors. Fourth-class bricks are mostly used as aggregates. They are used as aggregates for concrete, floors, or even roads.
3. FLY ASH BRICKS
A very unconventional type of brick, which is made from industrial waste such as fly ash, cement, or stone dust. They have gained popularity over clay bricks because of their environment-friendly aspects. They are very attractive and have a pleasant external appearance.
They have the same colour as cement and are uniform in size. Due to its uniform shape, it reduces the use of mortar by almost 30-45 %. A plaster coat is not necessary, putty or POP can be applied directly over the brick surface.
Fly ash bricks have a very high compressive strength. Due to its high strength, minimum breakage and wastage take place during transportation.
Fly ash bricks do not contribute any extra weight to the applied structure and provide better protection against earthquakes. It improves its strength over time and gives sufficient stability to the structure. They absorb less heat. As a result, you experience a cooler house in summer.
4. CONCRETE BRICKS
In general, bricks made of concrete are called concrete bricks. Concrete is a mixture of cement and aggregate like sand, cinder, ash, etc. These bricks are formed in moulds and cured properly before using them. Concrete bricks are very versatile as they are made according to the required size.
They are generally used in making walls that may be internal or external. Concrete bricks provide an outstanding aesthetic external appearance. There are wide varieties of concrete bricks which are classified according to the material used as aggregate.
In the USA, cinder is used as aggregate material, and hence they are called cinder blocks. In the United Kingdom, it is called breeze blocks, as the breeze or ash is used as an aggregate material. In the Philippines, concrete bricks are commonly referred to as hollow bricks. Meanwhile, in New Zealand and Canada, they are called concrete blocks.
Some companies use clinker as the aggregate material so, it is also known as clinker blocks. Choice of aggregates includes industrial wastes, ash or bottom ash, recycled consumer glass, etc. Concrete blocks can be shaped as traditional masonry style or big staggered blocks.
Most of the concrete bricks are made hollow. These hollow caves in concrete bricks are made to reduce weight and form an interconnected space between brickworks. Concrete bricks are generally referred to their size by width, which come in modular sizes of 4-inch, 6-inch, 8-inch, and 12-inch. Read Also: 12 Different Types of Brick Cuts Used in Brick Masonry.
5. ENGINEERING BRICKS
Engineering bricks are typically used where low water porosity, higher strength, and resistance to acids are of utmost necessity. Engineering bricks are defined as, “Fire-clay bricks that have a dense and strong semi-vitreous body and conform to defined limits for water absorption and compressive strength”.
The superior quality of engineering bricks or Class A engineering bricks is generally blue because of the higher firing temperature. Class B engineering bricks are generally red in colour. With respect to strength, Class A engineering bricks have a very high strength of 125N/mm2 and absorb water as low as 4.5%.
Class B engineering bricks have a strength of around 75 N/mm2 and water absorption of less than 7%. Engineering bricks are generally made to improve the structural intensity and technical strength of the building.
Engineering bricks do not provide any external aesthetic look but are mostly useful in the practicality of the structure. If you need to have a better look and feel of your building, then choose clay brick to enhance the look. But, engineering bricks are most important for your building’s strength and water resistance properties.
Generally, engineering bricks are used in places where strength and damp-proof constitution is needed like – manholes, sewers, retaining walls, and general groundwork. Engineering bricks have smooth surfaces and perforations throughout the body. They are widely available in blue color (Class A) and red (Class B).
6. CALCIUM SILICATE BRICKS
They are popularly known as sand-lime bricks. Calcium silicate bricks are made of sand and lime. Calcium silicate bricks are mainly used for ornamental works and other masonry works. Sand lime bricks are very popular in European countries as well as in Africa and Australia. In the case of India, the usage of calcium silicate bricks are most familiar in the state of Kerala. Calcium silicate bricks contain about 88-92% of sand and around 4% of clay.
Before making these bricks, it should be considered that the sand used should be free from any impurities like organic matter, soluble salts, etc. The clay is used to provide a smoother surface and it help the brick in pressing. The proportion of lime content in calcium silicate bricks ranges from 8-to 12%. The water used should be pure and should not contain impurities like soluble salts.
Generally, some pigments like Carbon black, Ochre, Iron oxide, etc. are added to provide some color. During the manufacturing of calcium silicate bricks, firstly proper proportions of sand, lime, and pigments(0.3% to 3%) are mixed thoroughly and about 3-5% of water is added. With the help of a machine called a rotary table press, the mixture is then molded into bricks, using mechanical pressure to press the bricks. The pressure ranges from around 31.5 to 63N/mm2.
After this process is completed, the bricks are placed into autoclaves for the final stage. In the autoclave, saturated steam pressure around 1.6 N/mm2 is used with rising temperature. These conditions initiate the reaction process. Silica in sand and calcium in lime reacts to form a crystal-like compound known as calcium hypo silicate. This whole process takes around 7 to 16 hours.
The color and texture of these bricks are uniform and required very less mortar for plastering work. They have 10 N/mm2 compressive strength. So, they are suitable for multistoried buildings as well. Calcium silicate can also be seen as blocks and tiles, and provide flexibility to workers to attain desirable shapes and designs. As they are free from impurities, so the effects of such impurities are also less. Solar heat is absorbed less by these bricks. These bricks provide fire resistance and water-repellent properties as well.
More coming soon…..
Read Also: